So in comes a Calcutta 400D; locked up and the level wind is actually displaced into the RH sideplate. Something has come adrift, and I reckon I know what…
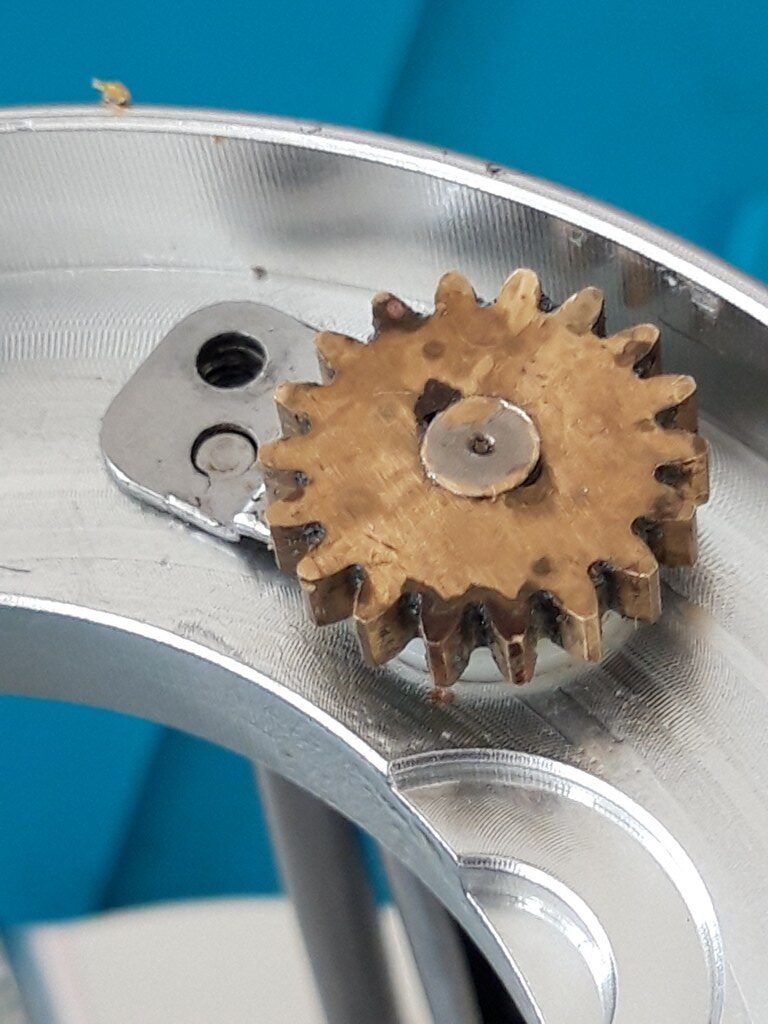
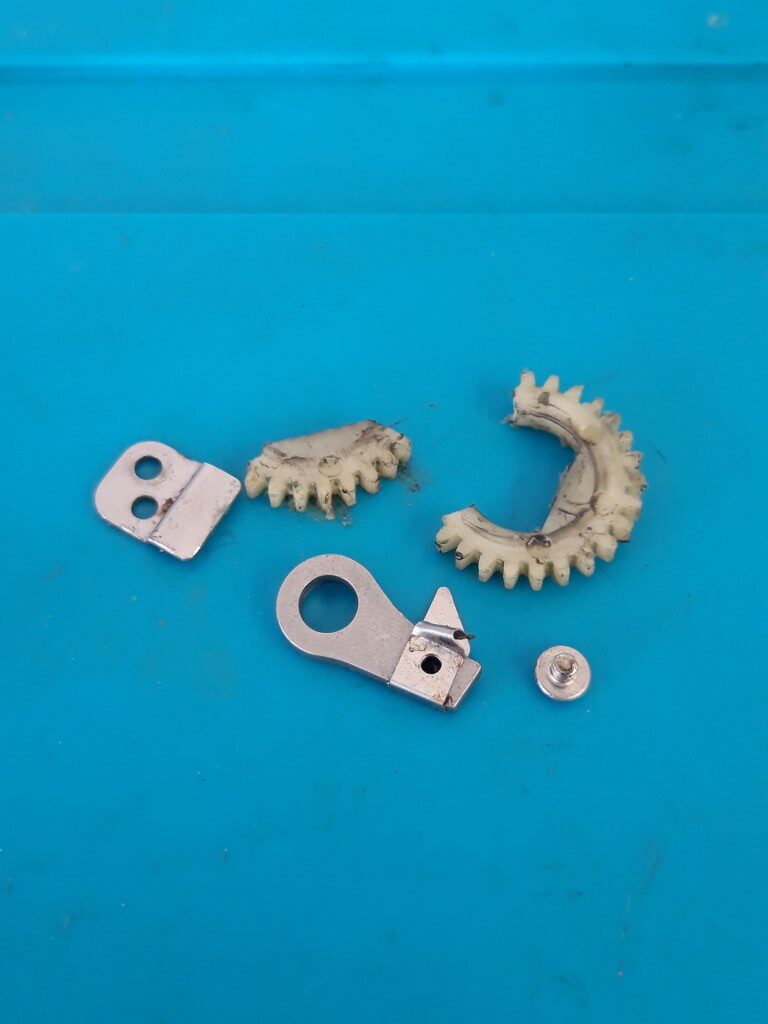
Carnage had ensued as the plate worked it’s way around the sidecover and took out the LW idler gear and the AR pawl. The hole in the frame where the plate is fixed has been stripped out…. bugger! So what can be done?
Drill it out and rethread it to M2.5/M3? That means a bigger screwhead under the bronze LW gear, will it fit there? Will the same problem occur in the future?
How about we put a stainless steel M2 helicoil insert in there?
Whaaaat?
Yes! Thread inserts actually come in sizes DOWN to M1.6!
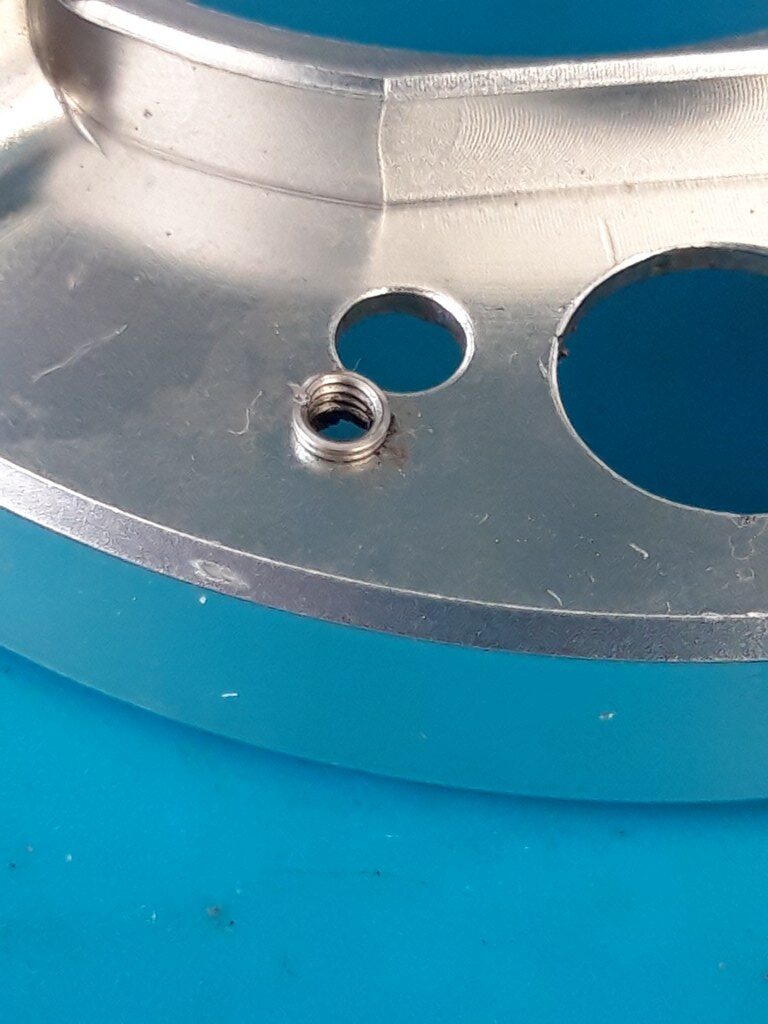
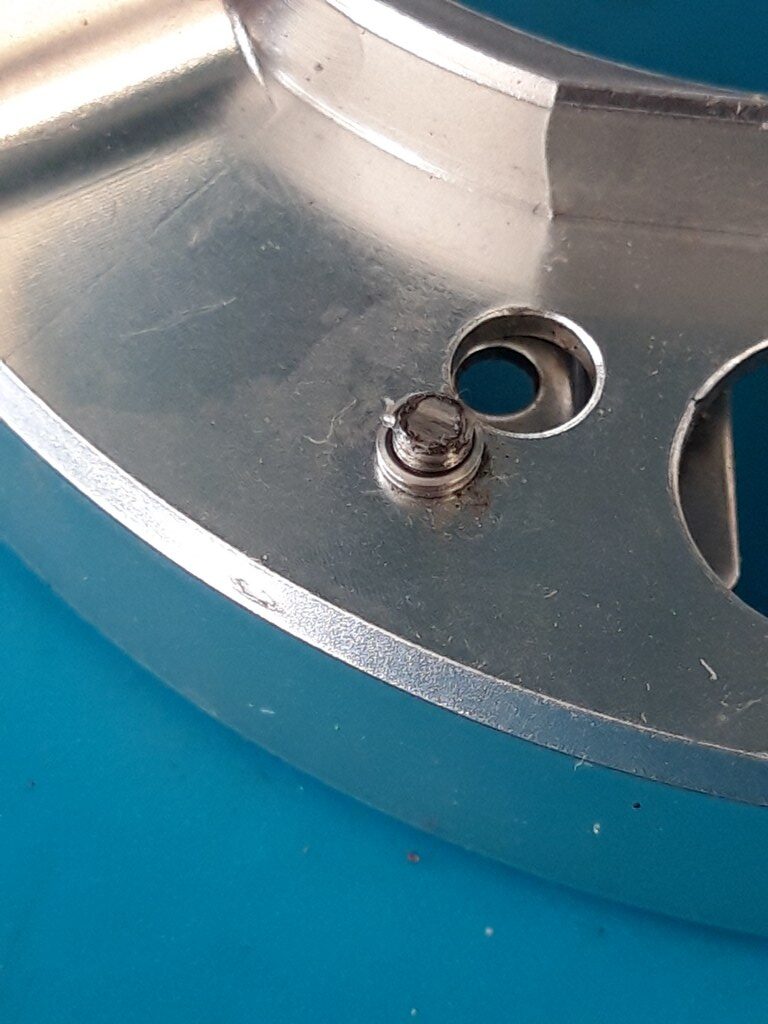
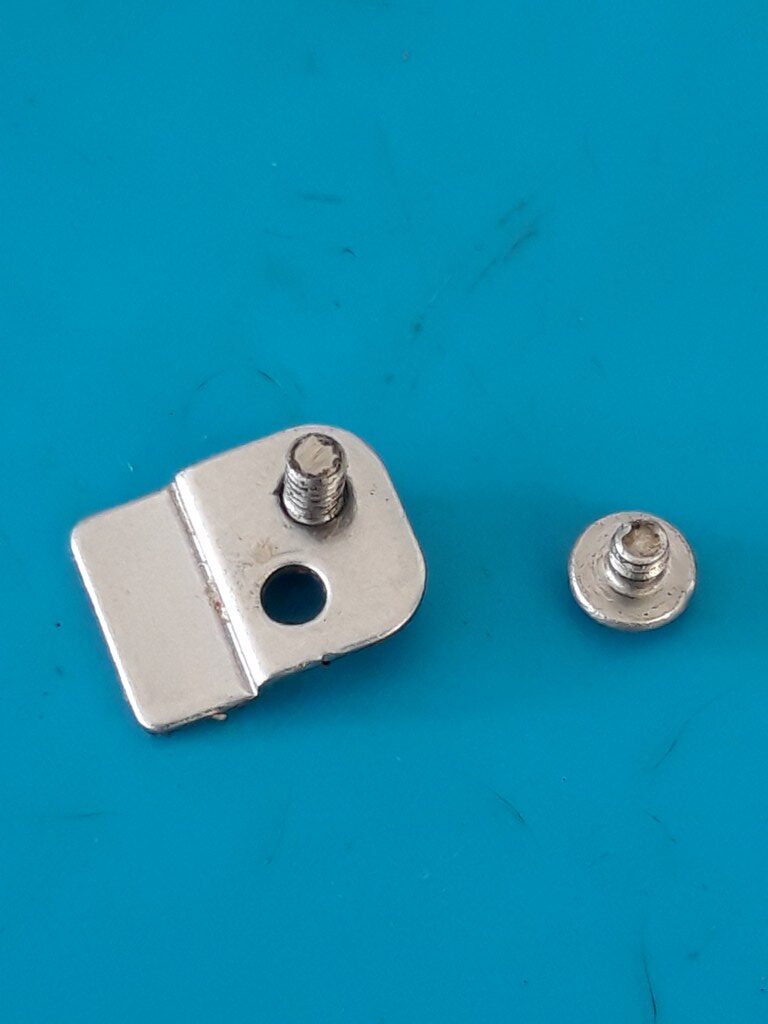
The frame on most of these Calcuttas is around 1.5mm thickness where the plate locates, and the thread is cut straight into the alloy. The pitch is .4 on these M2 screws, so there is minimal engagement of a stainless screw into an aluminium frame. Look at the length of that original screw: there are only about 2.5 threads on it to start with, let alone what is left after it goes through the fixing plate! Between galvanic corrosion, salt water and ham-fisted tightening it is a big ask for the fixing to hold. I can’t tell which (or if all) of these factors led to this screw stripping out. Note that I have left some of the M2 helicoil insert that I have fitted to sit proud of the frame to give the new (longer) stainless M2 screw something to hold on to (and yes, it still clears the line guide!). A drop of Corrosion X and maybe a bit of locktite screwlock and it should be good, there is no need to go hard on these screws as there is no real load on them. The picture below shows the technique for these small screws: two fingers and just nip them up!
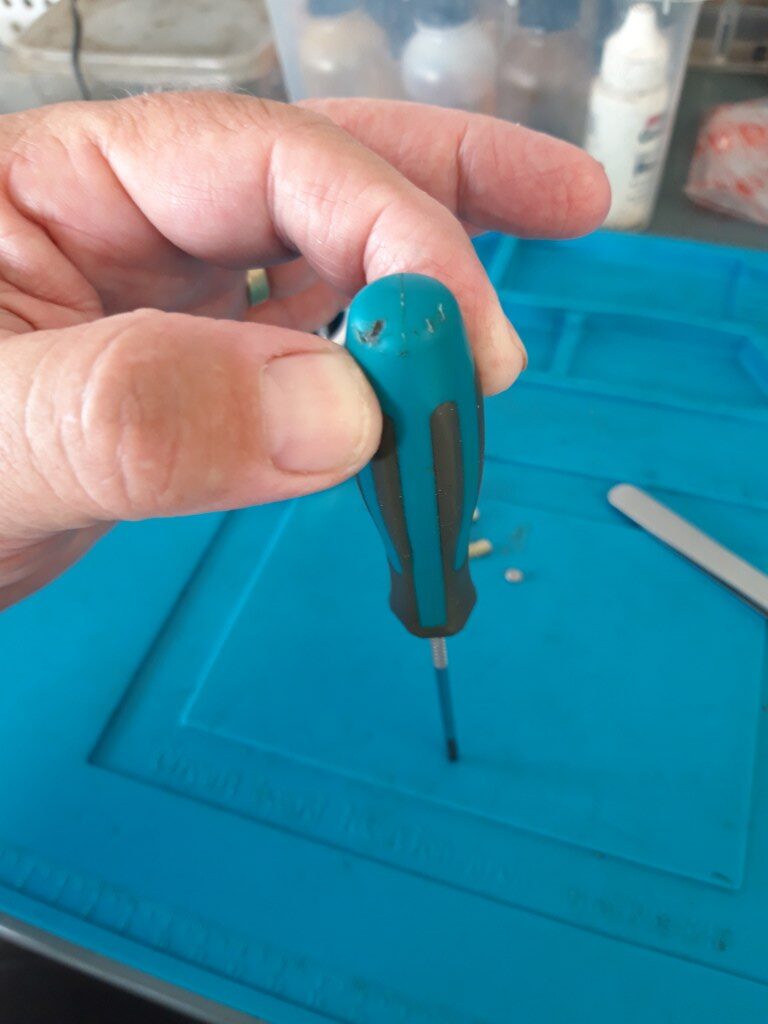
That’s all they need! Use finesse people, stainless steel threading into aluminium can end in tears if you are not careful.
Take care of your gear everyone!